By DLA Aviation Public Affairs
July 5, 2011
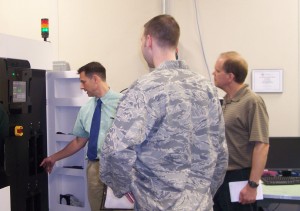
Members of DLA Aviation Casting and Forgings Program Assistance Team discuss mold patterns and sand cast parts.
New technology in sand castings is helping Defense Logistics Agency Aviation provide military services with parts in less time, with lower scrap, and lower cost, said Dale Roberts Aviation Casting and Forgings Program Assistance Team program manager.
Many DLA Aviation metal parts are made from “sand castings,” where molten metal is poured into sand molds created by pressing wood patterns into a special sand that is held together with binding materials to retain the shape.
“These sand castings have an advantage, in that very complex internal shapes can be created inside of a casting using internal sand molds that are removed after the metal cools by breaking up the sand, and pouring it out of an available opening. Though possible, it may not be practical to ‘hog out’ complex internal spaces by machining that are easily produced using sand castings. However, skilled craftsman traditionally construct the patterns using wood and similar materials, which can take weeks, and is an expensive process.”
As part of DLA Aviation’s castings program Roberts, along with Air Force Capt. Alex Mol, and Keith Sturgill with Advanced Technology International, met with the John Danko, president of Danko Arlington to see firsthand new technology his company is implementing to meet the challenge of producing specialized aviation castings economically, Roberts said.
“DLA Aviation has visited their facilities in the past, as part of the AFCAT bus trips that bring DLA Aviation personnel to foundries and forges to see the technology and meet with people in the industry,” Roberts said. “Since the last visit in September 2010, they made the decision to adopt new technology that allows an even faster response to the needs of DLA customers.”
Danko said his business uses rapid prototyping where drawings are converted to physical patterns by computer: “We now use stereo lithography to convert a computer-based model of the geometry and dimensions into a ‘3-D print’; an exact pattern of the needed part,” Danko said.
“It is like watching the ‘replicator’ on Star Trek, as the computer literally prints a 3 dimensional object before your eyes, including voids, passageways and internal spaces that may not be visible,” Roberts said. Roberts said with this new system, “there is no need to use precious work space for storage of traditional patterns that are used infrequently, when it can be printed out as needed for a small production run, then disposed of or recycled.”
“This new equipment will enable the company’s existing Foundry, Pattern, and Machine Shop Divisions to quickly and accurately produce mold patterns for parts (and the sand cast parts themselves) in days instead of weeks, and at much lower cost,” Danko said. “The use of computer aided design to move paper to production helps to create optimum patterns, reducing scrap. It is exciting using new technology in a traditional industry.”
“The computer model really simplifies the making of the casting molds. You can handle it just like the real thing, but on a computer screen. You can turn it in 3-D and look at it from every angle,” Roberts said.
Roberts said if a craftsman made a physical wooden casting model, it would take weeks compared to making one with a computer with a few clicks from a computer mouse.
“The benefit to DLA and the warfighter is that rapid prototype of patterns reduces lead time and cost. For infrequent buys in small quantities, ‘economies of scale’ works against us; However reducing set up costs with new technology helps us reverse that trend,” Roberts said.